He does things the old-fashioned way, but that doesn't stop him from innovating. In Gaillac, in the Tarn region of France, Cédric Franques and his sister Sophie run Imprimerie Rhode, a family business where letterpress finishing is neither nostalgia nor demonstration, but daily production. In fact, they account for 20% of sales at this 10-strong printing works.
The Chambre de Métiers du Tarn et d'Occitanie (Tarn and Occitanie Chamber of Trades and Crafts) has chosen to recognize this long-standing, innovative and operational practice by awarding it the title of Master Craftsman Printer, the only one of its kind in Occitanie.
Imprimerie Rhode, a remarkable workshop
The idea of applying for this prestigious title came from a teacher visiting with students. Seeing the gilding machines in operation, she mentioned it to the Chambre. Contact was made. November saw the start of the application process, with the presentation of projects. "It was intensive, especially on paper" remembers the master craftsman printer.
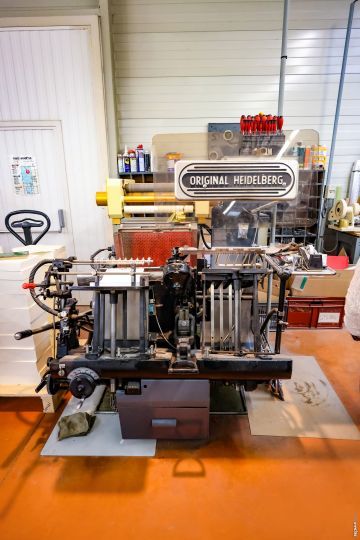
In January, La Chambre visited the printing plant a few months later. She discovered a multi-purpose production site with integrated finishing, where Epson plotters coexist with offset and letterpress presses.
"We do almost everything, from digital to offset to die-cutting. And since 2019, we've integrated finishing. The only thing we don't do in-house is laminating and varnishing, as well as glue-stitching."
Old-fashioned gilding, a skill inherited from his grandfather
Hot foil stamping is carried out on letterpress presses. "My grandfather taught me the trade. Today, there aren't many of us left doing this gilding. It's a job that's being lost, because the equipment is no longer up to standard, so only company directors can use the machines." Embossing and embossing are also regularly combined with metallic finishes.
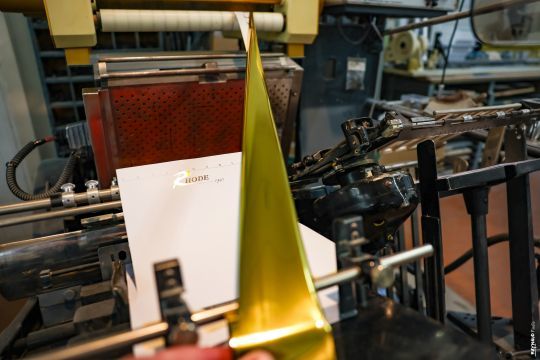
Announcements, reception cards, letterheads, menus: the applications are numerous, for a variety of customers, from private individuals to high-end establishments. And ince the post-Covid period, demand has grown even stronger. "Customers want media that stand out from the ordinary. We're seeing a real return to quality."
Two years of development for scratch-off ink used in gilding
And these aren't the only finishes for which the printing house stood out. Another more discreet but equally masterful process caught the attention of the Chambre des métiers: a scratch-off ink applied not by screen printing','www.printindustry.news/search/serigraphy');" class="lien-auto-article" href="https://www.printindustry.news/search/serigraphy">screen printing, but by hot foil stamping. "This keeps costs down and the minimum number of copies down compared with screen printing."
This process took him two years to develop, researching films and application processes: "The scratch-off films offered by suppliers only worked on a specific paper, with a specific backing, and the result was often random. From there, I thought about developing this product." For the past year, Rhodes has been offering its scratch-off ink on a subcontracting basis, and today it produces an average of one pad per week for this type of application, particularly for tombolas.
Towards a certified zero-waste printing plant
After being awarded the title of Maître artisan imprimeur on May 5, Cédric Franques is now pursuing another initiative: the Zero Waste label. The workshop has already launched several initiatives, including the recycling of stretch film, which is now used to stuff down jackets. At Gaillac, graphic tradition continues to coexist with committed technical choices and lively production.