Heidelberg has just released the new generation of offset presses, the Speedmaster 2020 With these new machines, the German manufacturer is launching the Plate to Unit system, which enables fully automated plate management from CTP to offset plate unloading.
We asked Hubert Viger, Head of Technical Expertise and Applications at Heidelberg France, to explain how it works...
GraphiLine : Why did you develop an automated printing plate management system? What does it bring to a printer?
Hubert Viger: While printing volume is expected to remain unchanged over the next few years, the average job length will continue to decrease. Driver fatigue has become important, and to increase productivity we needed to optimise the handling of the printing plates on the press.
What is the Plate to Unit?
The Plate to Unit is a transport system for offset plates from the plate carriage at the margin to and through the various printing units.
This system was the missing piece of the puzzle! We already had all the other components for automated plate management: IntelliStart 3, which generates a job queue, Prinect Scheduler, which schedules production, the Prinect Plate Pilot for automatic plate output, and Nela, the fully automated plate stacking and bending station.
Pure mechanics is actually only half of the system.
What degree of automation can be obtained from this complete system?
In workshops with a low level of automation, 23 intervention points are required from plate making to wedging. We have reduced the entire process to three manual interventions.
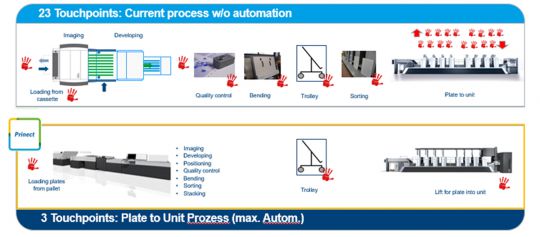
How does this work in practice for the operator?
This starts with planning the optimal job sequence using the Prinect workflow from Heidelberg. Relevant factors are the optimization of setup times, delivery dates, etc. The job data is sent to the PTC.
Secondly, the pallet of blank offset plates is loaded into the CTP (1 of the 3 manual interventions). The entire printing plate production process is automated (quality control, bending, etc.) until the plates are placed directly on the plate carriage in the order of the Prinect optimized work sequence. In this system, all plates and carriages are identified and tracked by barcode.
The carriage will then be moved from the prepress shop to the print shop in a buffer zone (2nd of 3 interventions) while waiting for printing.
When the printer arrives at the next job sequence, he sees on the Prinect Press Center controller which plate cart he needs and where it is located.
All he has to do now is take it (3rd and last intervention) to the Plate to Unit cabinet next to the margin.
The Plate to Unit automatically manages the feeding of the plates in the right order to the right printing units by transporting them one by one over the press. The automatic unloading will place the plates back on a trolley.
A few years ago we were talking about 10 jobs a day, today we're more like 10 jobs an hour. This system, which changes the way we manage the entire offset production process, is perfectly suited to many of today's and tomorrow's markets.