The photopolymer plate
Flexography is a direct printing process, widely used in the packaging industry, especially for the manufacture of labels. However, its manufacturing techniques remain unknown compared to other industrial reproduction methods.
The printing form, also known as the plate, matrix, or sole, is raised and varies in thickness from 0.78 to 6.35 mm. The use of thin plates offers a sharper print, a reduced dot gain, and an optimal ink transfer.
euros in its raw state, the flexographic plate consists of a photopolymer plate, topped by a carbon layer intended to receive the negative of the image or the composition to be engraved.
In the past, rubber was the raw material used in the manufacture of flexographic plates, but today it is largely replaced by synthetic resins allowing a finer linearity and thus the reproduction of a greater number of details.
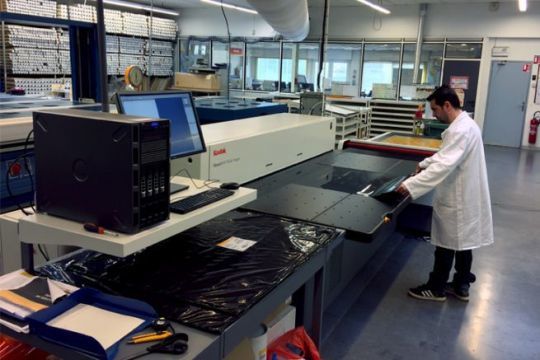
Sunstroke
The production of a conventional plate takes an average of 30 minutes. The elements of the negative film are engraved by laser on the carbon layer, then the exposure of the plate by UV rays shapes the material by cross-linking: the openwork parts of the negative are exposed and harden. The laser engraving of the plate is very powerful, because it makes it possible to reproduce complex and finer screens than by older processes.
Nowadays, it is possible to eliminate the negative manufacturing step by connecting the computer directly to the platesetter.
Washing and drying of the flexo plate
The cleaning of the uninsulated plate is usually done with solvents. When it is immersed in the washer, the plate loses its last traces of carbon and the printing form appears.
The drying operation is the last stage of the manufacture of a flexographic plate. Carried out at a temperature ranging between 50 and 60°, the drying produces a setting in relief of the zones of impression and remains a delicate stage because the plate, sensitive to heat, can undergo a retractation if the parameters are not respected.
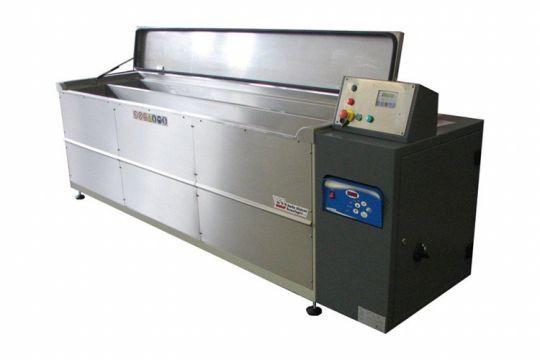
Cutting of the plates
Depending on the photo-engraver, the dimensions of the photopolymer plate in its raw state can be 1m x 2m. To save a maximum of material, the plates to be produced are amalgamated, then cut to correspond to the final format, ordered by the printer.
Tips for preserving a flexo plate
The flexographic plate is sensitive to light. To prolong its life, it is important to clean it properly with water after each use and not to expose it to light for more than a few days: the material will harden within a week.
Too much pressure when rolling can also damage the plate and wear it out more quickly. Once the job has been printed and washed, the plates must be stored for the next print run. To do this, it is recommended to store them in opaque kraft envelopes with foam sheets between each color (and therefore each plate) to protect them from shocks and rubbing.
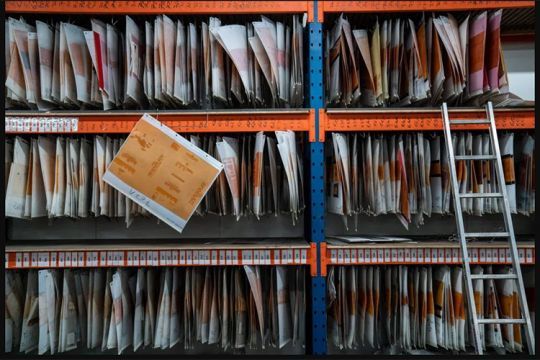